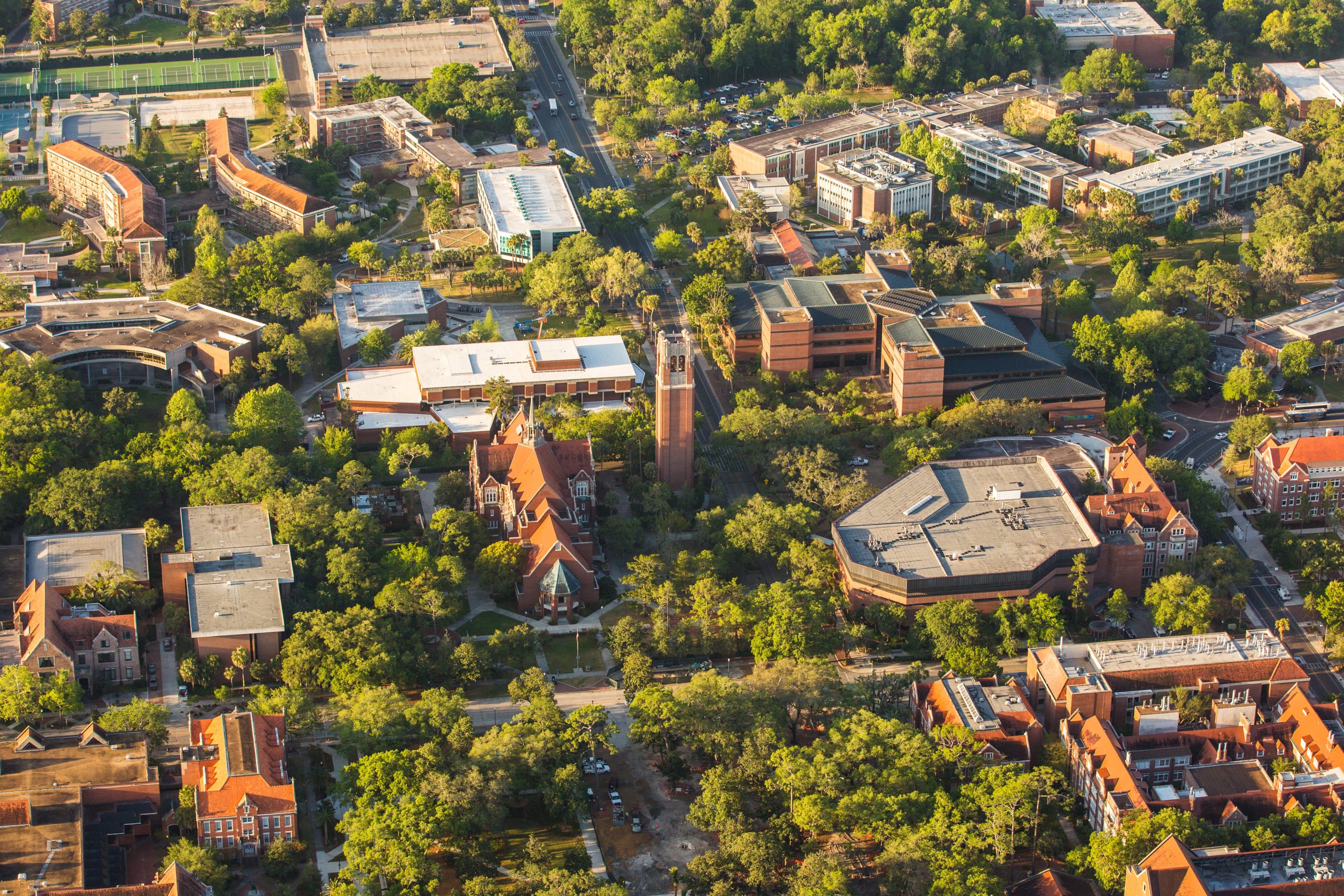
IEQ New Construction and Renovation
In some instances this policy varies from other more traditional guidelines such as local codes. It is the intent that when this policy is at variance with other accepted standards, the more stringent shall apply.
Requests for exceptions or variations to this policy should be brought to the Environmental Health and Safety (EH&S) division for discussion and approval. Please contact the EH&S IEQ Coordinator at (352)392-1591 with questions regarding this policy.
This IEQ policy applies to all projects involving new construction, renovation or remodeling. Renovation or remodeling projects that do not involve the installation of or extensive modifications to an HVAC system are exempt from the sampling requirements contained in this document.
EH&S will review plans and project specifications to determine whether IAQ baseline sampling is required.
EH&S will investigate any concerns dealing with indoor environmental quality issues during a construction or renovation project and will work to resolve the concerns to the satisfaction of all affected parties.
Design professionals and project managers need to make sure the requirements of this policy are followed and arrange to any required air sampling.
When sampling for IEQ parameters is required, it is the responsibility of the design architect/engineer or project manager to arrange for the pre-occupancy sampling by EH&S or by a qualified outside firm. If sampling is to be done by an outside firm, the sampling plan must be developed by an American Board of Industrial Hygiene (ABIH) Certified Industrial Hygienist (CIH) and submitted to EH&S for review and approval before the field work is conducted.
EH&S can perform the required sampling for a fee that is typically charged against the project budget.
Time to collect and analyze the required samples must be accounted for in the project schedule. Depending on the size of the project, sampling will typically take at least a day to complete and up to 14 days to receive results and to complete a final report. Sampling cannot occur until there is an accepted test and balance of the HVAC system and until all installation of building finishes including the furniture is complete.
Ultraviolet light (UV) lighting arrays may be used to control microbial growth in drain pans and on coil surfaces in an air handler. UV-C systems must be specifically designed for use in an air handling unit.
The use of other types of in line air cleaning or treatment devices must be reviewed and approved by EH&S prior to installation. Examples of such devices include but are not limited to negative and/or positive ion generators or electrostatic precipitators.
Devices specifically designed to purposely emit ozone into the air stream of any space are prohibited.
Installed air handling equipment must be protected from dust, insect, vertebrate, moisture and microbial contamination. Air handling equipment, including ductwork, which becomes contaminated during construction must be cleaned or replaced prior to start-up.
Duct supply air systems shall not be operated without filters in place. Filters used in air handling equipment operating during construction shall have a minimum dust spot efficiency of 35% (MERV 8 or 9). All filter media shall be replaced with 80% (MERV 13) filters before the serviced space is occupied.
Alternatively, before applying interior finishes, the HVAC system should be run 24 hours per day for a minimum of 3 days at a stable temperature and at a relative humidity below 60%. The HVAC system will remain in 24 hour operation throughout the installation of finishes.
Vinyl wallpaper and other water impermeable coverings or coatings shall not be permitted on the interior side of exterior walls.
Preference is to be given to the use of low volatile organic compound (VOC) emitting paints, glues, carpets and other furnishings and fixtures.
Construction and renovation projects adjacent to occupied spaces present additional IEQ concerns. It is not uncommon for odors, noise and dust from projects to create problems for the adjacent occupants.
Exposures to even low levels dust or chemical contaminants can cause or aggravate asthma, allergies, headaches and mucous membrane irritation in building occupants. The following specific recommendations are intended to prevent these problems.
Areas under renovation shall be separated from adjacent occupied areas by full height hard wall barriers. The barriers are intended to block the transmission of dust, odors and other contaminants from the work area to the occupied spaces.
The work area shall be maintained at a slight negative pressure relative to the adjacent occupied space. Negative pressure can be achieved through adjustment of the HVAC system or by the addition of additional exhaust ventilation in the work areas.
A test and balance of the HVAC system will be required following project completion when pressure adjustment is made through manipulation of the HVAC system.
Regular (daily) housekeeping shall be performed to prevent the tracking of dust and debris from the work area into occupied spaces.
Odor or contaminant producing equipment set-up outside of the interior work area must be located away from outside air intakes or building entrances. Examples of such equipment include roofing tar pots, portable gas or diesel powered engines and portable lavatories.
Workers involved with the project must follow the requirements of the University’s smoking policy.
Material Safety Data Sheets (MSDS) shall be maintained on site for all chemical products used during the renovation or construction process.
The specific parameters to be measured, their maximum allowable concentrations and the acceptable monitoring methods are noted in Table 1. A minimum of one sample set is required to be run for each occupied floor or for each 25,000 square feet of floor area. A sample set is defined as the collection of three formaldehyde samples and one each of the other listed and applicable parameters. Sample duration shall be for 4 hours. Shorter sampling durations and variations in sampling methods may be allowable but approval must be received from EH&S on a case by case basis. The use of colorimetric indicator tubes for sample collection is not permitted. All samples shall be collected between 3 feet and 6 feet from the floor to represent the breathing zone of the occupants.
Parameter | Maximum Allowable Concentration | Monitoring Method |
Formaldehyde | 0.027 parts per million (ppm) | NIOSH 2016 |
Particulates (PM10) | 50 micrograms per cubic meter (ug/m3) | Direct Reading Instrument or NIOSH 0600 |
Total Volatile Organic Compounds (TVOC) | 500 ug/m3 | EPA TO-15 |
Carbon Monoxide (CO) | 4.0 ppm | Direct Reading Instrument |
*4-Phenylcyclohexene (4-PCH) | 6.5 ug/m3 | Listed OSHA Method |
*4-PCH monitoring is only required if latex backed carpeting is installed
Table 1 Baseline Sampling Parameters
Sampling is to be conducted prior to the occupancy of the building. The HVAC system must be operating in its normal design mode and all furnishings should be in place during sampling. Any touch-up painting or the use of materials containing volatile organic compounds including custodial cleaning products should cease at least 24 hours prior to sampling. The sampling techniques are sensitive to even low levels of chemicals which may result in reported concentrations that do not accurately reflect conditions in the building.
The vacuuming or sweeping of floors should cease at least 2 hours prior to the start of particulate monitoring.
Parameter | Acceptable Levels |
Carbon Dioxide | |
Carbon Monoxide | |
Relative Humidity | 40% – 60% |
Temperature | 68°F – 74°F Winter Range 70°F – 78°F Summer Range |
Table 2 Indoor Comfort Parameters
Indoor radon levels should also be measured following occupancy of a new building. Levels are expected to be below 2 picocuries per liter (pCi/L). Radon sampling can be arranged by contacted the EH&S Radiation Safety office.
Any concerns or questions regarding this policy or IEQ issues in general should be forwarded to the EH&S IEQ Coordinator at (352)392-1591.